The NHAI is all set to lauch 3D automated machine guidance (3D AMG) technology in highway construction in the country. For the first time, 3D AMG technology will be used for the construction of the Lucknow-Kanpur Expressway by the National Highways Authority of India (NHAI).
This technology is expected to double the speed of construction of the highway as well as enable the officials and contractors of NHAI get a direct update of the speed of work on their phones and computers. The 63 km long Lucknow-Kanpur Expressway is the first such project in India in which this technology will be used.
AMG, uses data from sources such as 3D engineered models to guide construction equipment during earth work and paving operations. The use of AMG improves construction efficiency, quality, and safety while reducing schedule, cost, and the environmental impacts. This Executive Summary will show how deployment of AMG in the right situations can benefit all stakeholders during roadway construction project
How AMG works
AMG, a downstream application applied to highway construction projects provide construction efficiencies through enhanced location referencing. AMG involves using construction equipment mounted with onboard computers. Using a combination of 3D modeling data along with global positioning system (GPS) technology, AMG provides horizontal and vertical guidance in real time to construction equipment operators. AMG assists agencies and contractors in finishing projects in less time and with lower overall cost while providing higher quality and safety.
AMG equipment has the potential to achieve designed grades on the first pass, reducing impacts on budgets and schedules compared with traditional staking. Using data from technologies such as 3D modelling in combination with GPS, automated machine guidance can increase productivity by up to 50 percent on some operations and cut survey costs by as much as 75 percent. Project-level optimization occurs when all elements built into and associated with the roadway are fully designed into the 3D model.
Contractors, recognizing the vast opportunities to reduce costs with AMG, are taking advantage of these technological innovations. State agencies expect AMG to make more efficient use of already limited resources for construction. Industry-leading departments of transportation (DOT) recognize that potential advantages and cost savings are abundant.
AMG and MCS
AMG, sometimes used synonymously with Machine Control Systems (although MCS might imply no need for human control), uses enhanced location referencing to provide accurate horizontal and vertical positioning for precise grading, milling, or paving. Bulldozers, graders, milling machines, and paving machines can all be programmed to use this technology when performing grading or paving tasks in the field. Moreover, scrapers, excavators, and trenching machines can be equipped with AMG for a wide variety of earthwork.
A machine that uses AMG references the position of the cutting edges or pavement molds using GPS satellites, robotic total stations, lasers, or combinations of these methods. It calculates the finished-grade for that location using an electronic model of the proposed constructed facility that resides in its onboard computer. Then, it adjusts the cutting edges or pavement molds automatically for small differences in elevation or provides the cut or fill amount via the computer-user interface to the machine operator for large differences in elevation. Typically the machine operator manually grades the surface until it is close to design specifications, then switches to “automatic” for finish grading.
The data inputs from a digital terrain model and associated data preparation and formatting are important parts of a successful AMG application. The model data must be passed on to the contractor, who often transforms it into AMG compatible format. Contractors might hire a data preparation consultant to provide the final machine files for use in the field or might develop their own model if not originally provided by the DOT.
Guidelines for quality assurance and quality control are required throughout the process for both design and construction. AMG construction specification often focus upon geodetic control, location referencing and checking, machine calibration, and final construction check procedures, frequencies, and tolerances. Such specifications also usually address model development responsibilities and, potentially, data flows between owners and contractors
The advantages of AMG include reducation in construction costs, reduced schedules, environmental friendliness, increased quality and increased safety.
(courtesy: US Department of Transportation; edited by A. Harikumar)
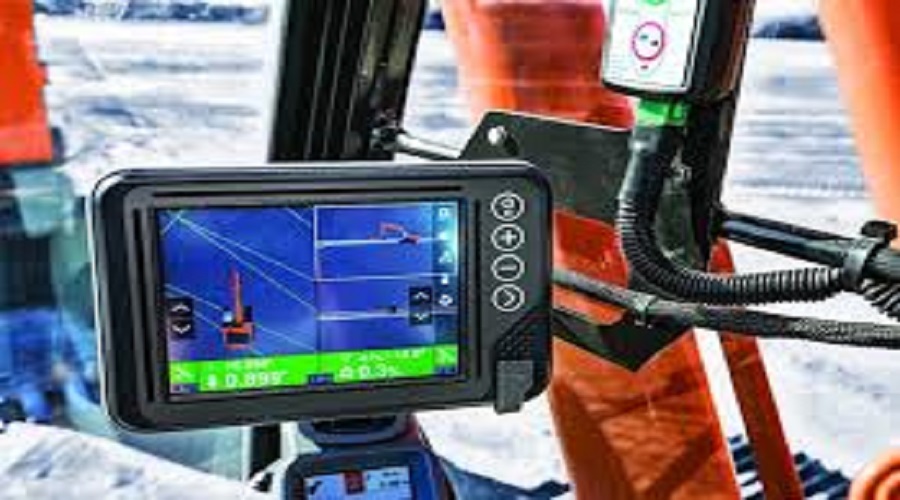